A seasoned and experienced orchard manager once said the following about the apple harvest:
We can’t put them back on the tree once they’ve been picked."
This statement epitomizes the challenges facing apple growers, pickers, shippers, and work crew managers at harvest season around the world.
Due to the short harvest window, and the massive quantity of apples to be picked, it has been practically impossible to manage and assess whether workers are picking the right apples at the right time to meet the ever changing and ever increasing demands of the global marketplace. In the past, most orchards have relied solely on the opinions and qualitative standards of orchard managers to “course-correct” pickers when they are choosing the wrong size or color of apples.
The challenge is that over this very short period of harvest time, orchard managers must rely on hundreds of employees and temporary or contract laborers to perform the most important action of the year - choosing and picking apples of the right size and color. A skilled apple picker can pick an average of 12 boxes a day. That’s six tons of apples for every picker and 120 tons over one shift for a typical work crew of 20 people.
The massive volume and the fragility of the apples makes sorting for color, weight and size before storage nearly impossible. Using calipers and weigh scales, orchard or crew managers can quantitatively measure only about .00003% of the apples picked. Until recently there have been no tools that can quantitatively measure the color profile of the apples, meaning color metrics must be assessed from a manager’s best guess at the time of picking.
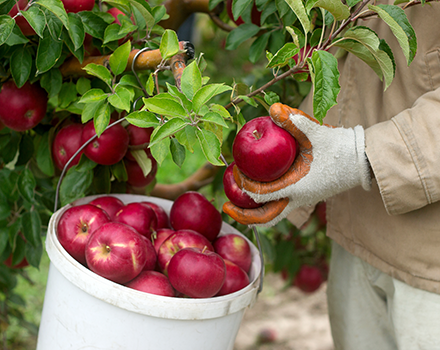
This lack of data on what is being picked in the orchard is one of the biggest pain points for orchard operations managers. Apple growers, packers, and shippers cannot match their produce supplies to the demands of the global market if they are constantly unsure of the supply coming from the orchard. Furthermore, the sheer volume of picked apples makes sorting before storage almost impossible, as orchard managers rush to harvest and store as much produce in as little time as possible.
The storage of these tons of harvested apples presents an additional challenge for growers. Orchard managers are continually looking for better solutions so they will have a better idea of what they are putting into storage. Depending on the storage facilities available to them, growers may store their commercial apple harvests for up to one year.
Post harvest tools for apple storage come in a variety of forms. Controlled Atmosphere Storage is a sophisticated technology, controlling multiple aspects of the storage unit’s climate. Where traditional cold storage maintains temperature levels, CA storage controls the atmosphere of the storage unit right down to the oxygen level. “In CA storage, apples are sealed in an environment that is around 2 percent oxygen where temperature, humidity, nitrogen and carbon dioxide are all carefully regulated.” (For reference, standing air has an oxygen makeup closer to 21%.) The reduced oxygen levels essentially slow the ripening process by making the fruit dormant.
Another popular storage innovation, SmartFresh is mixed with water and released as a vapor into the storage unit. The active ingredient, 1-methylcyclopropene (1-MCP), is similar to ethylene (the hormone that causes fruit to ripen) and blocks the apple’s ethylene receptors, preventing the fruit from ripening.
The cost of placing fruit into storage is high, and once the seal on a storage unit is broken, the apples will begin to ripen almost immediately, greatly reducing their shelf life. When the contents of a storage unit are unknown, growers are faced with the expensive decision of which unit to open, at the risk of opening the wrong unit and wasting valuable inventory. Thus, apple growers, packers, and shippers are constantly looking to technological and operational innovations to reduce this uncertainty within their multi-billion dollar organizations. Produce quality control measures that can be done in the orchard would save a huge amount of time and money for farmers by giving them greater insight into their stored inventory.
Examples of innovations include various models of digital calipers and scales, bin scanners like Croptracker’s Harvest Quality Vision (HQV), and digital tracking tools like Orchard Hands. HQV is currently the only solution for colour grading in the field. Growers are increasingly looking forward to these and other agtech innovations to help them make better and more accurate decisions, based on greater quantitative and statistically accurate produce quality data directly from the orchard.
Interested in learning more about Croptracker? Learn more about our Farm Management Software, or book a demonstration to schedule a meeting with our product experts.
And as always, if you're ever stuck, never hesitate to e-mail us at support@croptracker.com or Live Chat with us by clicking the green speech bubble in your bottom right-hand corner. We're always happy to help you make the most of Croptracker to make your farm more efficient, safer, and more profitable!