For any sector to thrive, disruptive technologies and innovations must fall into place. In agriculture, farmers constantly seek new ways to increase the yield per acre, and at the same time, deal with rising input costs. Investment and innovation in robotics has been a big focus in agriculture recently, with reports from Wintergreen Research projecting an anticipated $16.3B market size by 2020.
In this piece, we’ll take a look at the most innovative advances and emerging robotic technology in the agriculture sector, and explore their impact on farmers.
The Technology Behind Advancing Robotics
A few technological advances in recent years have led to the development of many of the robots listed below. Many agricultural robotic advancements use machine vision technology to avoid hazards, identify crops, and even determine if they are ready to be harvested. Machine or computer vision typically involves a camera or multiple cameras feeding information to the robot that allows it to locate and access the crops around it. Machine vision makes it possible for robots to perform tasks like weed picking, growth monitoring, harvesting, sorting, and packing.
Satellite location systems like GPS have also made many of the advances in agricultural robotics possible. Robotic farm equipment often relies on GPS information to position and locate themselves on farms. Autonomous field plowing, seeding, or navigating tractors and equipment may use a combination of computer vision sensors and GPS to navigate and act as the driver in robotic plowing trucks.
Another technology employed in agricultural robots is machine learning. Machine learning provides an advanced method of identifying collision paths that can help autonomous vehicles learn to adapt and avoid new or unexpected hazards in their paths. It also enables picking and quality control robots to learn as they go, and to develop the best methods for identifying and executing their tasks.
Robots in the Field: Autonomous Tractors
Self Driving
In the case of autonomous farm equipment, machine vision and movement sensors work hand in hand to avoid obstacles while navigating the field. The robots create a virtual 3D model of the surface, and with the help of high-resolution cameras, they’re able to navigate freely. Movement is, however, not automatic as it depends on what parameters they are programmed to avoid or maneuver through.
John Deere tractors have standardized the autonomous features of their tractors. AutoTrac, the company’s self-driving technology, is based on GPS, satellite corrected technology, and comes standard with self driving technology and a modem for all units sold in the US. The next step? Integrating computer vision and machine learning to help the tractors identify new obstacles or animals in their paths.
Seeding
Automated drone seeders are mostly used in forestry industries right now, but the potential for more widespread use is on the horizon. Planting with drones means very hard to reach areas can be replanted without endangering workers. They are also able to plant much more efficiently with a team of two operators and ten drones capable of planting 400,000 trees a day.
Autonomous precision seeding is a relatively new technology that combines robotics and GIS mapping. By generating a map of a field and including information about soil properties such as density and soil quality, autonomous seeders are able to seed more accurately than traditional broadcast spreading seeders or drone seeders.
Weeding
Combatting weeds and making sure crops have room to grow is a constant struggle for farmers. Recently, FarmWise, a San Francisco startup, raised close to $20 million to develop an agricultural robot that deals with weeds, using a 100% organic method, by picking them. Using computer vision and a variety of mechanical tools, the robot plucks out individual weeds instead of using chemicals. “A single FarmWise robot can weed outcrops to feed a medium-sized town of approximately 400,000 people,” said Sebastian Boyer, the company’s CEO.


In Australia, Engineers and researchers from the University of Western Australia (UWA) and the University of Sydney have developed a mechanical weeding machine of their own, to combat high rates of herbicide resistant weeds across the continent. Their six metre wide “weed-chipper” uses tines to till out weeds that are detected using commercially available weeding cameras such as the weed seeker.
In the case of the weed chipper, the weedseeker sensors detect the weeds, but rather than applying a spray, the weed-chipper tines activate to mechanically remove the weeds from the earth. The company Naio Technologies has had a similar weeding robot on the market since 2017 and many more competitors will continue to emerge as the technology improves.
Spraying
Similar to manual weeding robots, smart sprayers are typically paired with computer vision cameras to identify weeds for targeted herbicide applications. Sophisticated systems can even identify specific plants and activate only the relevant application nozzles. This means less waste, reduced herbicide resistance, and more efficient application across fields.
Picking
Strawberries, like many berries and tender fruits/veggies, demand a very intensive harvesting program. Harvesting these crops require a lot of labour and time, both of which are often in short supply. If a farmer is unable to harvest in time the crop will go to waste. The harvest process is quite intense, and farmers often run short of workers due to the backbreaking nature of the harvest.
The strawberry market in particular is currently estimated at $16 billion, and it’s no surprise that tech companies have already developed and used robots designed explicitly for strawberry harvesting, with an eye to expand into other hard to handle crops. Perhaps the most common is Agrobot™, an agri-tech firm currently developing a wide range of robots to help solve farmers’ harvesting challenges.
One of Agrobot’s flagship projects is a 24-arm robotic harvester, designed to pick strawberries. Agrobot uses machine learning technology to identify and measure the ripeness of the berries. Once identified, the robot cuts the fruit just above the calyx and then grips the stems to transfer them to harvest containers. In this way, the harvester never actually makes contact with the strawberries, minimizing the risk of damage or bruising.

In Canada and the US, where the farm labor crisis is hitting hard, Agrobot could harvest close to 20 acres in three days, as estimated in a report by CNBC. Agrobot is not the only strawberry picker; firms like Advanced Farm Technologies (AFT) and Harvest Croo Robotics have developed similar agri-robots that are already servicing some farms in California. As these machines prove their worth, more versatility in which crops they can handle will follow fast.
Robots In the Orchard: Harvest and Quality Control
Computer Vision Quality Control
Croptracker’s own computer vision system, Harvest Quality Vision (HQV) is an exclusive technology that allows growers to scan a bin of apples with a camera attachment, which creates a 3D model of the scanned fruit. From these scans, HQV analyzes the samples to determine the size, color profile, and quantity of apples scanned in just moments. HQV can replace traditional pre-sorting by sizing harvested fruit right in the bin, reducing handling and transport that can damage the fruit.
Robotic Harvesting
New Zealand based T&G global is working in partnership with Abundant Robotics in California on robots that could change the face of fruit harvesting. In a couple of years, the robot will work alongside human laborers to pick fruits during harvest.
Tests have already proven to be quite fruitful, and the system has successfully harvested apples. The robotic system utilizes soft-touch robotics and a lidar sensing system to detect ripe apples, leaving out unripe fruits during the picking process. The goal so far is not to replace human pickers on the farm, but to enable 24 hour harvesting.
Innovations in so called “soft” harvesting, where machines are equipped with delicate suction cups or padded grabbers are just one way growers are protecting their fruit during autonomous harvests. In 2016 developers at Abundant Robotics created the first vacuum harvester, which uses computer vision to identify apples and then sucks them through a soft hose at a rate of an apple per second.

Vision Robotics has also developed a similar system that involves a pair of agri-bots that work hand in hand. One robot uses 3D technology to map the farm area, gathering data that includes the location and size of each orange. The second robot is designed to pick oranges using its unique eight arms, guided by the 3D map given by the first robot to navigate and select the ripe oranges only.
These harvesting robots are still new but their potential for easing the problems of limited labour availability is great. So far the price tag on many of these robots if hefty and is not yet viable for small farm operations. We will see more harvesting robots on large orchards much more frequently in the coming years.
The orchard robots mentioned above use new technologies to gently handle fruit harvesting, but robots in orchards have been around for a long time. Tuthill Temperley, a company based in England, has been producing apple harvesting robots since 1969. These robots are used for harvesting cider apples so the need to be gentle with the apples is not necessary. Tuthill produces a few types of harvesters, one of which shakes the tree and catches apples that fall, another then sweeps the apples off the ground between the rows of trees.
Robotics in Non-Tradtional Farming
Robotic Greenhouses
One of the agricultural sectors with the most robotic innovations is indoor growing. Automated indoor agriculture is still a new phenomenon but some companies are making great strides into the industry by using fully automated systems. The company Iron Ox boasts of having the world’s first autonomous farm, clocking nearly 8,000 square feet. Inside the area doesn’t resemble your typical farm field. Instead, it is filled with massive hydroponic trays and two cloud-controlled robots that supervise the whole project. Leafy greens are the main products plus a couple of herbs like chives, parsley, and sorrel.
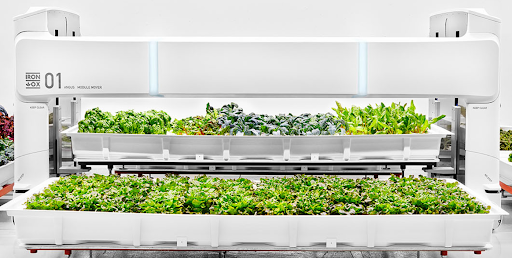
One of the robots uses sensors as “eyes” to analyze and pick the plants while the other lifts and transports the trays across the facility. Apart from the two, there are dozens of other on-site scientists (including other robots). A small automated farm like this could produce the same amount of yields as a one-acre of conventional farmland. All the plants in the farms are grown under specialized LED lights, and the facility claims to use 90% less water than conventional farming. The indoor farming industry will be an industry leader agricultural robotics.
Agricultural Drones
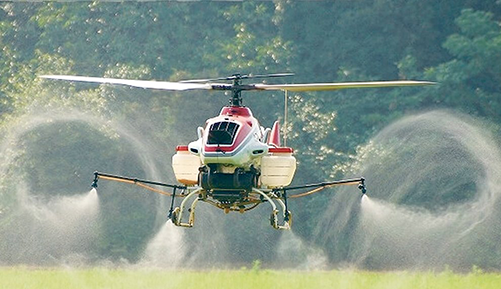
Beyond land-based robots, tech firms have also incorporated flying robots (drones) in farming, which facilitates precision farming during its operations. While drones are not necessarily an innovation, their use in agriculture is beneficial as they can be used in imaging, crop assessment, land monitoring, crop protection, land fertility, among others. NASA already has satellite technologies to monitor vegetation and successfully discerning unhealthy leaves using the normalized difference vegetation index (NDVI). However, drones fitted with such sensors can gather this kind of data both quickly and efficiently. Additional tweaks in the sensors could also help farmers get a more refined resolution allowing for quick evaluation. To learn more about drone technology in agriculture, check out our recent article here.
Conclusion
Innovation is essential in any sector and currently more relevant in agriculture than ever before. Embracing new technologies like robotics, machine learning, and computer vision will be a key factor in the changing face of agriculture worldwide. It will also reshape the definition of farmworkers, easing the workload and at the same time showing promising results in crop efficiency, increased yields, and managed input costs. Agtech is here to stay, and investors are more focused than ever on sustaining our economy through automation, robotics, vertical farming, modern greenhouse practices, artificial intelligence, and precision agriculture.
Interested in learning more about Croptracker? Learn more about our Farm Management Software, or book a demonstration to schedule a meeting with our product experts. Or if you liked this article, subscribe to our monthly newsletter!
And as always, if you're ever stuck, never hesitate to e-mail us at support@croptracker.com or Live Chat with us by clicking the green speech bubble in your bottom right-hand corner. We're always happy to help, so Croptracker can make your farm more efficient, safer, and more profitable!